
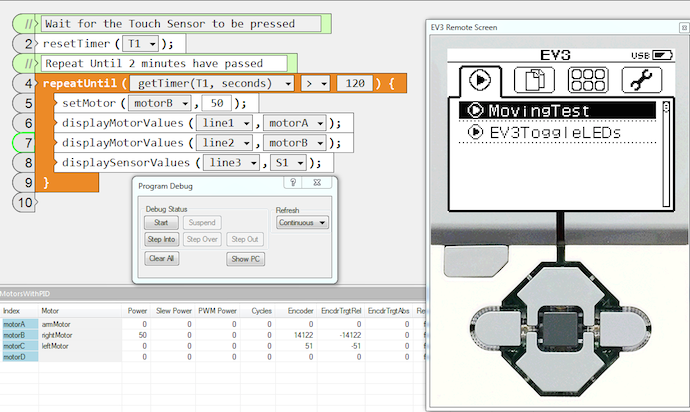
Created a successful design with two motors that press down on the pipet. Found another one, Eppendorf 200 ul.Ĭontinued working on the dispensing handling. The pipet needs to be tested for accuracy.Ĭhecked the pipet for accuracy, and it was way of. Solution might be to use the power function powers, which are smaller. Solutions might be: using two actuators, using a rail-design instead or adding more power to the actuator. The linear actuator works up to aboout 1,6 cm, putting a limit on how much the pipet can be pushed down. Worked on the primary handling operation with a very simpel design and set up the lab space. Introduction to robotics at Stanford Engineering.Creating own functions in RobotC By Albert W.Introduction to the RobotC programming language by Albert W.Articles on construction of trusses by TJ Avery.Peeron - LEGO sets part and inventory lists.The table below outlines the specifications of the machine.Ĥ20 mm (Width) x 375 mm (Depth) x 500 mm (Height)Ĩ5 mm (Width) x 200 mm (Depth) x 62 mm (Height) The finale documentation is not yet ready. Still it can be used to simple experiments and liquid handling. There are a number of limitations with the current design the robot has very wobbly up/down movements as can be seen on the videos below also the area available to work in is very small the robot does not error check the volumes it pipets.

The current project uses two Mindstorm NTX's, a 200μL micropipet, a couple of aluminum beams and a great deal of LEGO bricks. The goal of this project is to create an open-source liquid handling robot by using LEGO Mindstorm.
